Growing Living and Multi-Functional Mycelium Composites for Large-Scale Formwork Applications Using Robotic Abrasive Wire-Cutting
A biohybrid method that opens up new perspectives of working with living microorganisms at the large scale was developed in collaboration with Odico. We created a biological and digital fabrication pipeline for growing large mycelium material blocks, on-site robotic wirecutting, using mycelium materials as a multifunctional formwork, and implementing of self-healing properties of fungal organisms. As such, we also made two prototypes based on specific characteristics.
Multifunctional formwork
This biological and digital fabrication pipeline allows the (1) growing large mycelium material blocks, (2) on-site robotic wire-cutting, (3) using mycelium materials as a multifunctional formwork, and (4) implementing of self-healing of fungal organisms. The purpose of the research was to investigate the processing approaches and variable material handling for large bio-hybrid foam blocks. For the first time, mycelium materials were robotically wire-cut in situ, which resulted in two demonstrators. The robotic tool provided the freedom to shape and structure this novel bio-hybrid material and opened the possibility to make unique architectural modules. The research investigated two approaches for the application of fungal materials. Starting from an application-based intention, we tested the compatibility of the thermal insulating mycelium formwork with a concrete slab. As such, we combined two different materials with hybrid physical and architectural properties. Besides, we investigated the self-healing and living properties of mycelium components after the robotic implementation. The combination of microbiological systems with fibrous substrates created a unique class of bioactive composite materials with potential applications at the macro scale.
If we were to combine mycelium materials at the architectural scale with robotic manufacturing, there are several defining features to consider that were explored in this work for the first time:
1. New methods and processes are developed to work with large quantities of bulk material, with the possibility to cut the material according to specific shapes.
2. The regenerative biological materials composed of abundant components (lignocellulose and fungi) are fabricated at room temperature in non-sterile mild conditions, which is significantly different from synthetic materials fabrication.
3. The hybridization and functionality of the components serve more than one purpose.
4. The biological material can keep its properties of self-healing cracks and surfaces.
Living Materials
By drying the mycelium materials, the organism is heat-killed, thus missing out on crucial biological functionalities, such as its regeneration capacity. Therefore we investigated the potential to keep the mycelial organism alive during the whole fabrication process.
After the wire-cutting process, the two components were placed next to each other in an incubation room at a temperature of 26°C and relative humidity of 90%. Additional humidity was needed in this case because the sample dried out during the cutting and transport. The increase in humidity allowed the hyphae to continue to grow by tip extension and bridge gaps of 5mm between the two elements. While the organism continued to grow, it produced a dense network around the exposed fibres. Subsequently, the mycelium aggregated the substrate, undergoing differentiation to yield a well-insulated brown-greyish skin. The change of morphology affected the oxygen uptake, and after three days, the growth rate distinctly slowed down. After seven days of incubation, the two elements were fully connected. Finally, the block was air-dried in an incubator room at 30°C for one week and remained firmly attached.
Living materials coupled with robotic fabrication can play a role in the development of complex and custom-designed geometries that hold together without the need for mortar, glue or connectors.
Acknowledgements
This research was made possible thanks to the funding of the SB Fellowship of the Research Foundation Flanders [grant number 1S36417N (E.E.)]. The work was supplementary supported by an FWO long term travel grant [grant number V442219N] which financed my research stay at the Centre for Information Technology and Architecture (CITA), the Royal Danish Academy of Fine Arts Schools of Architecture, Design and Conservation.
Credits
Elise Elsacker, under supervision of Prof. Lars De Laet and Prof. Eveline Peeters / Vrije Universiteit Brussel / Department of Architectural Engineering and Bioengineering Sciences. The robotic wire-cutting setup was developed and performed by Asbjørn Søndergaard at Odico Formwork Robotics Aps, (Odense, Denmark). This work is licensed under a Creative Commons Attribution-NonCommercial-ShareAlike 3.0 Unported License 126.
Citation
Elise Elsacker, Asbjørn Søndergaard, Aurélie Van Wylick, Eveline Peeters, Lars De Laet, Growing living and multifunctional mycelium composites for large-scale formwork applications using robotic abrasive wire-cutting, Construction and Building Materials, Volume 283, 2021, 122732, ISSN 0950-0618, https://doi.org/10.1016/j.conbuildmat.2021.122732.
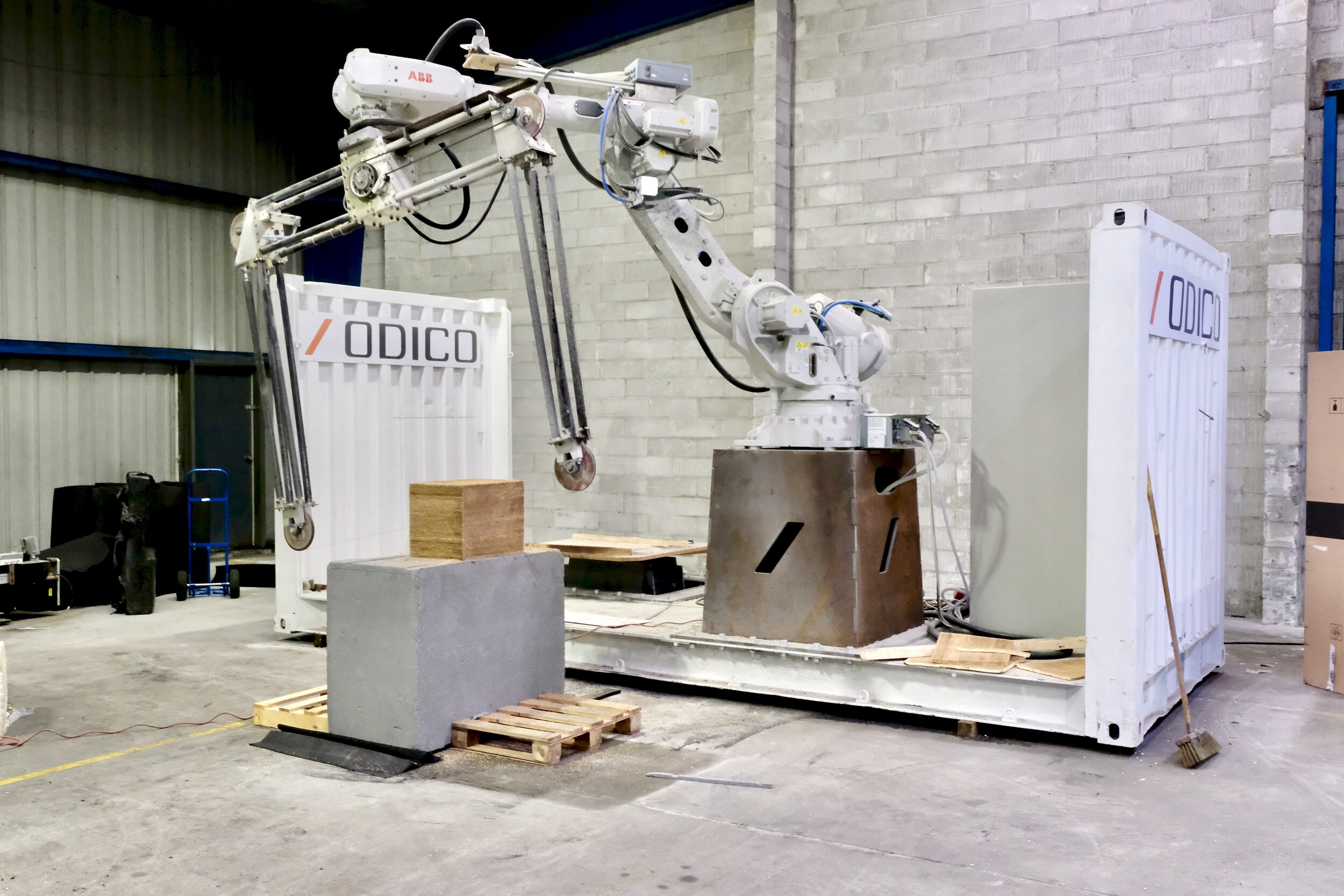
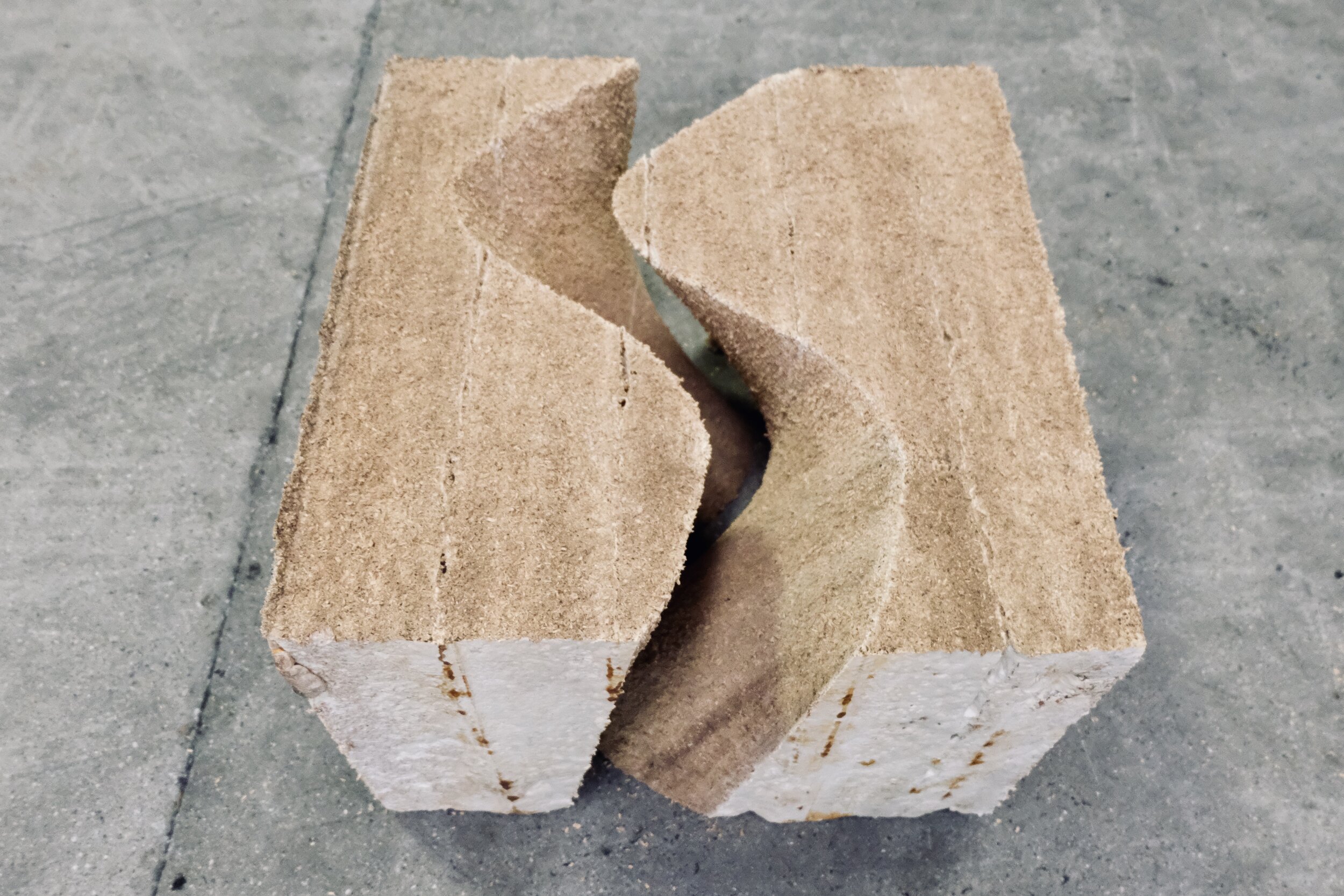
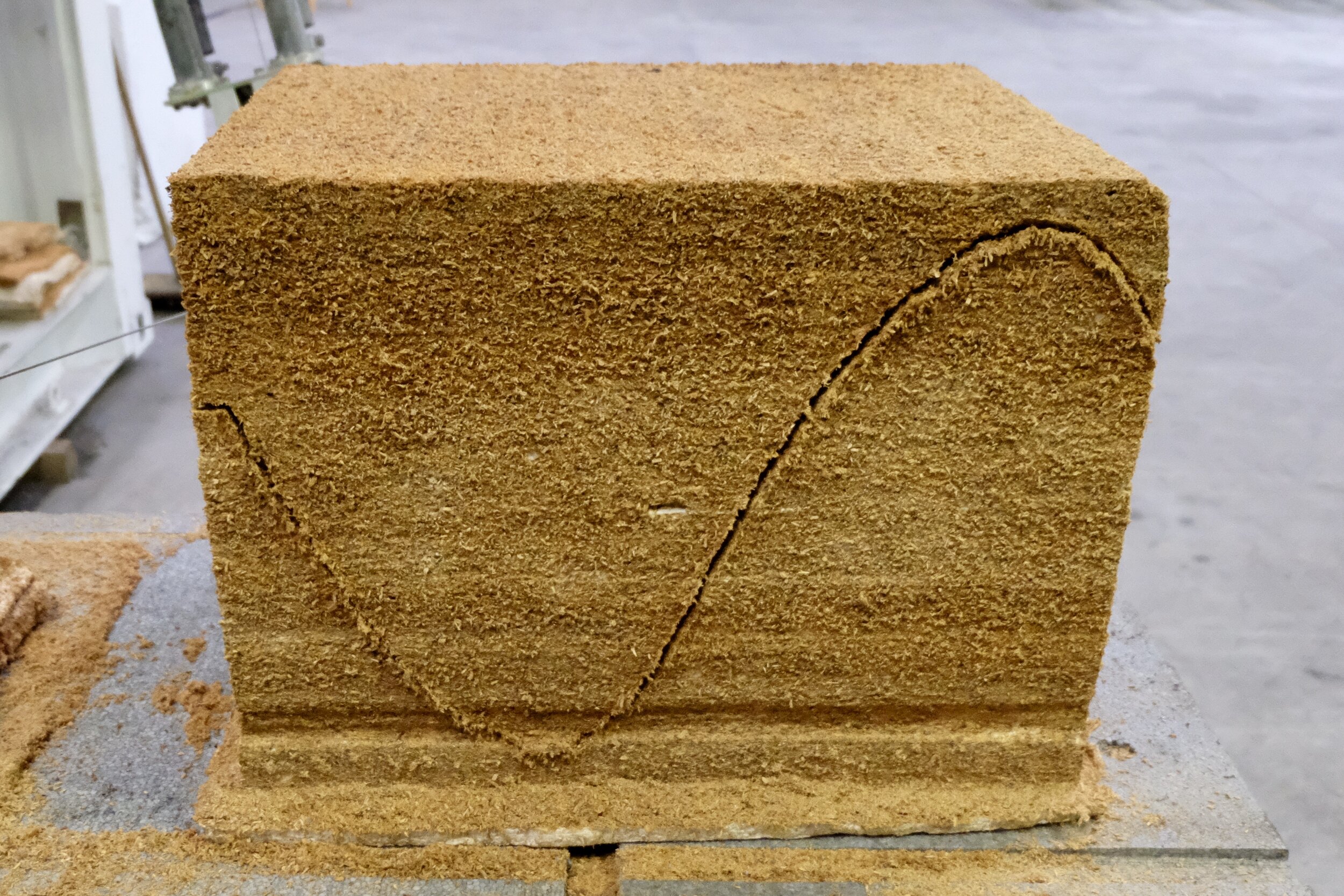
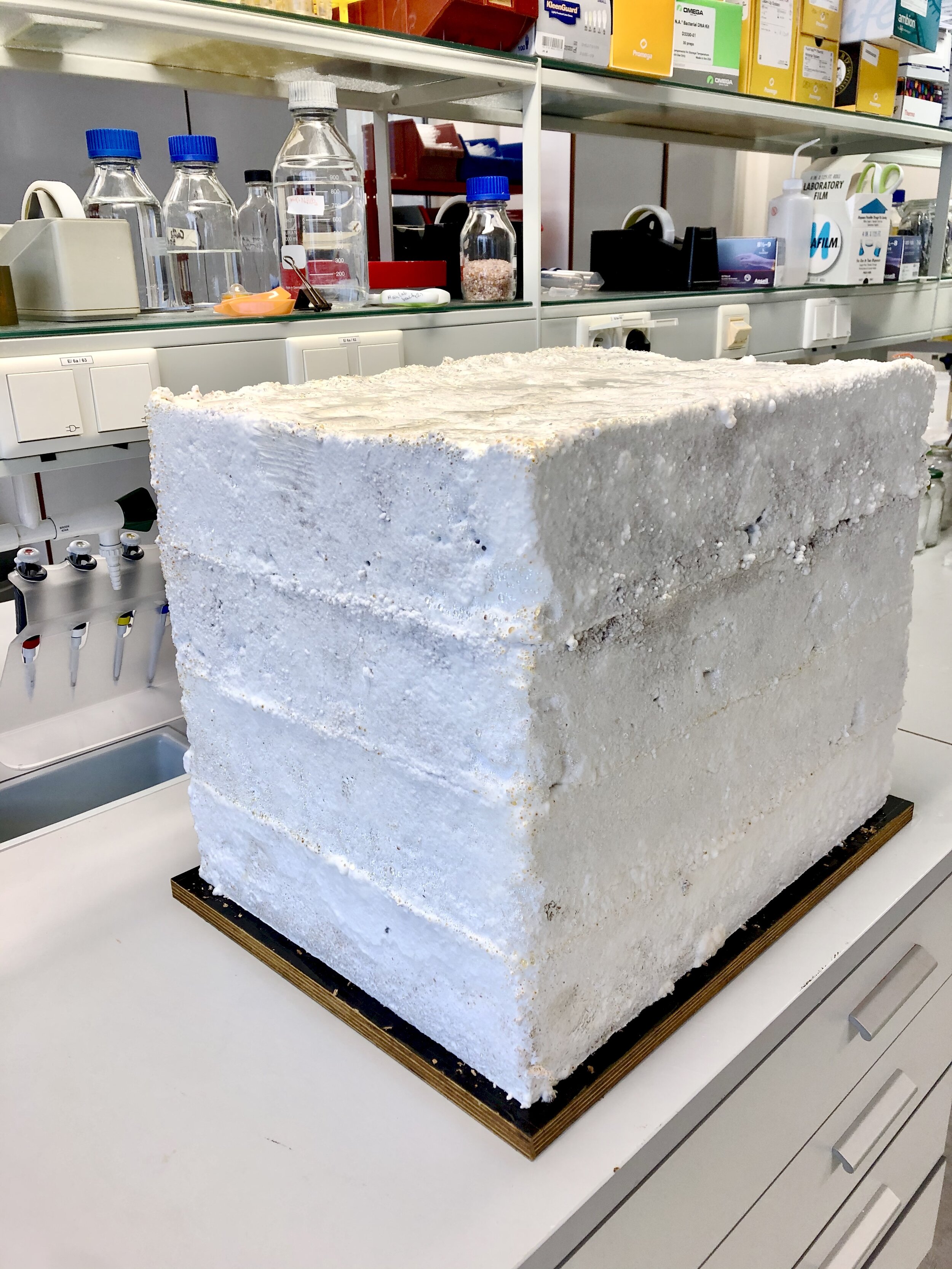
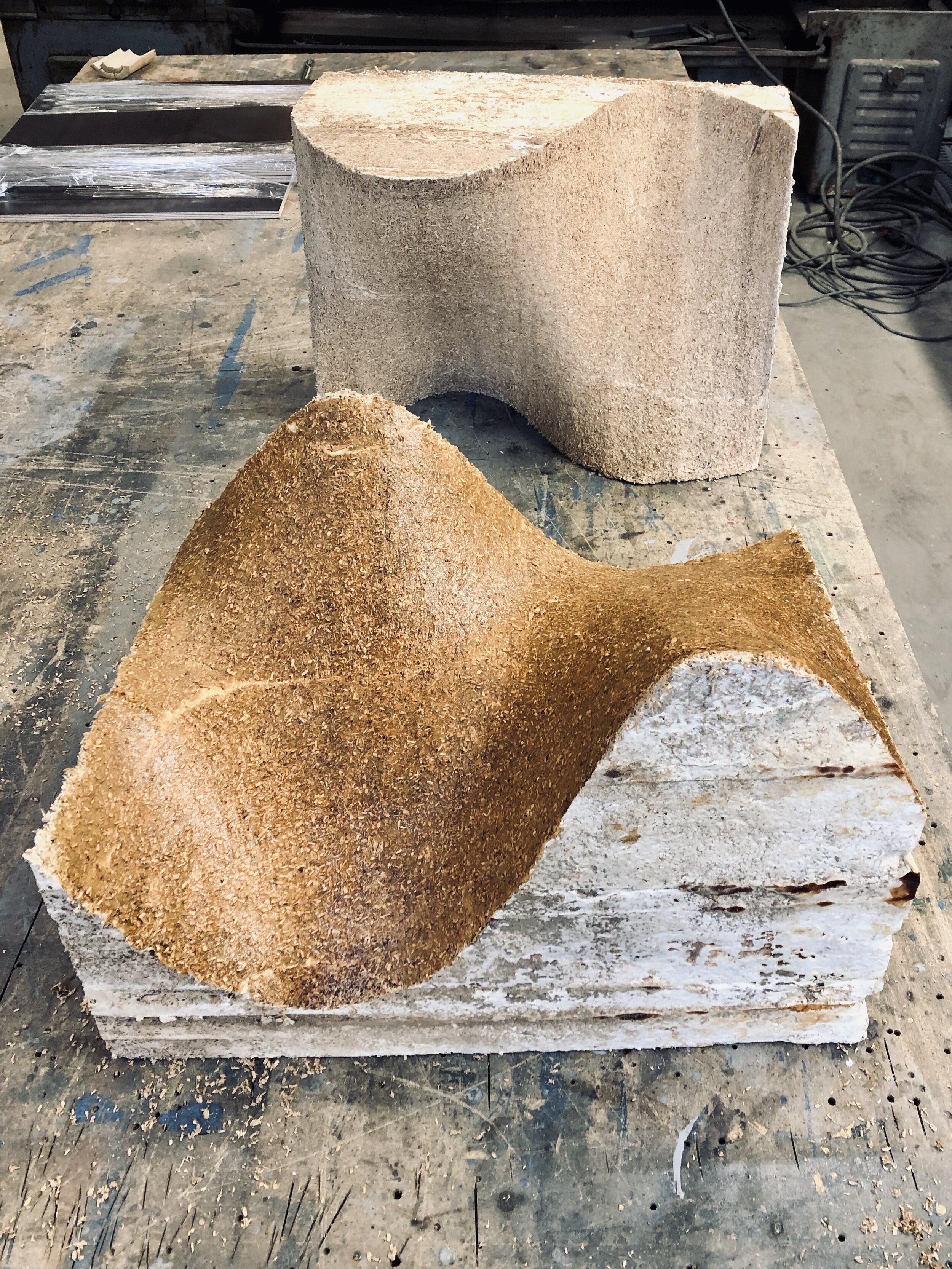
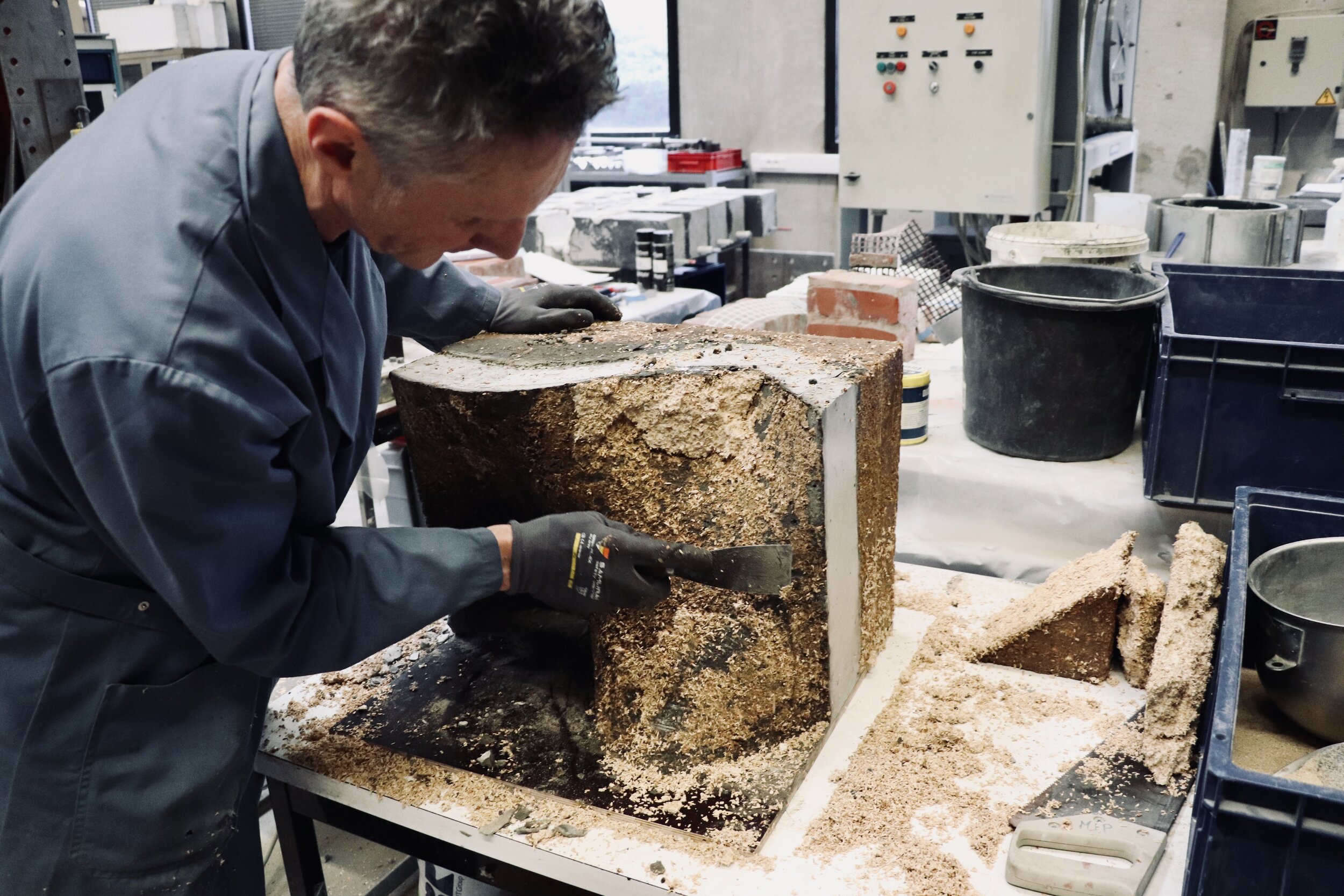
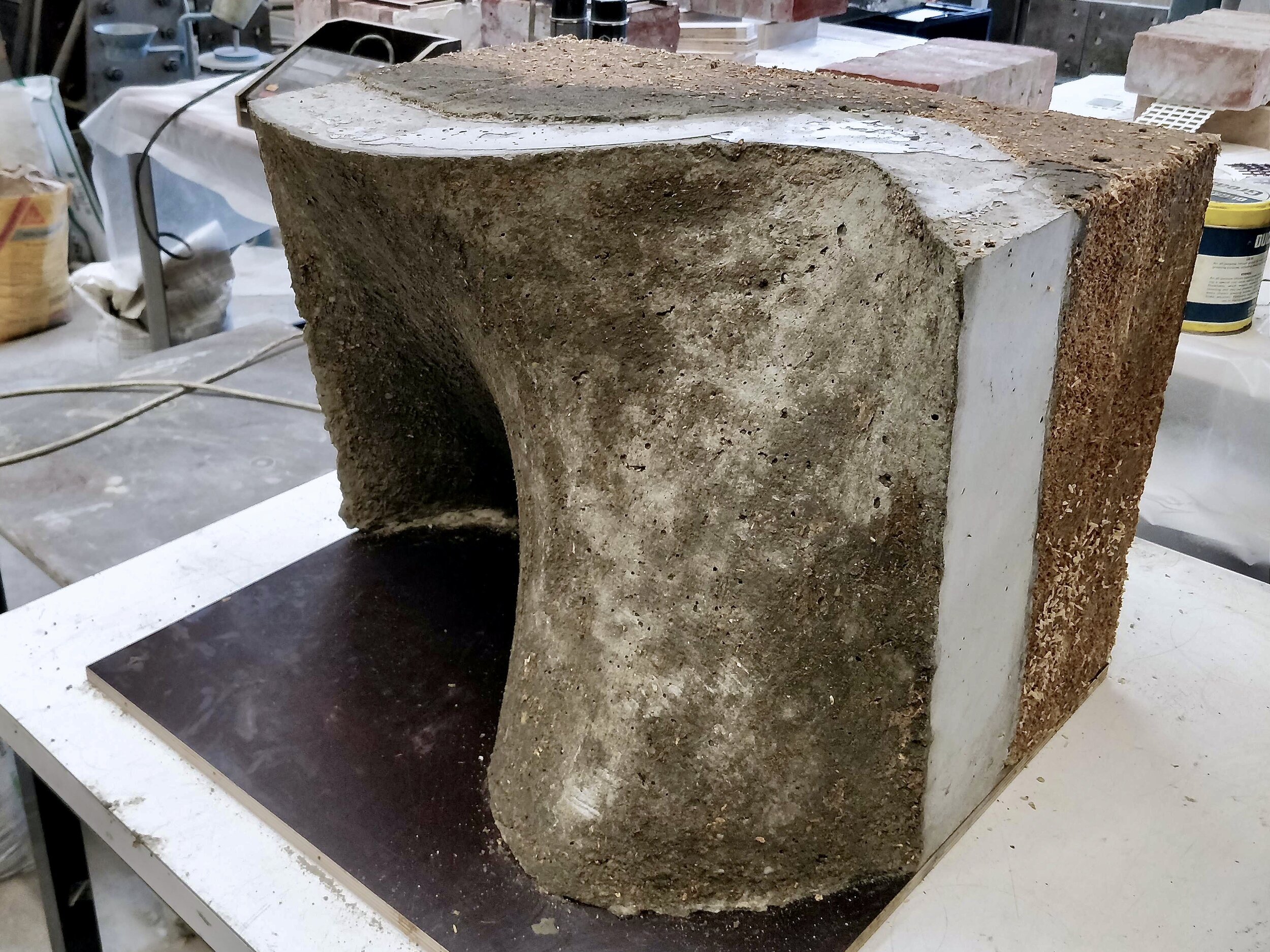
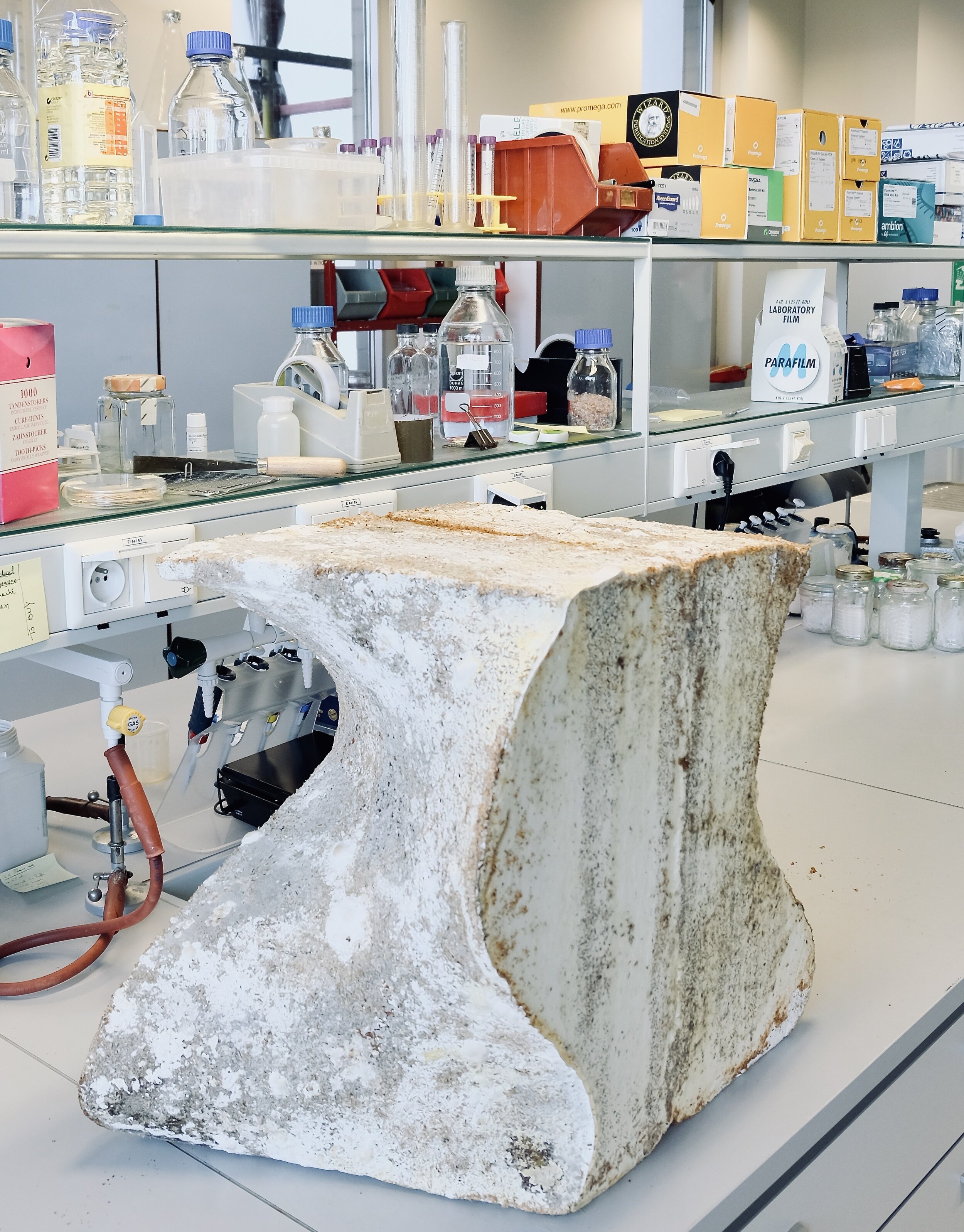
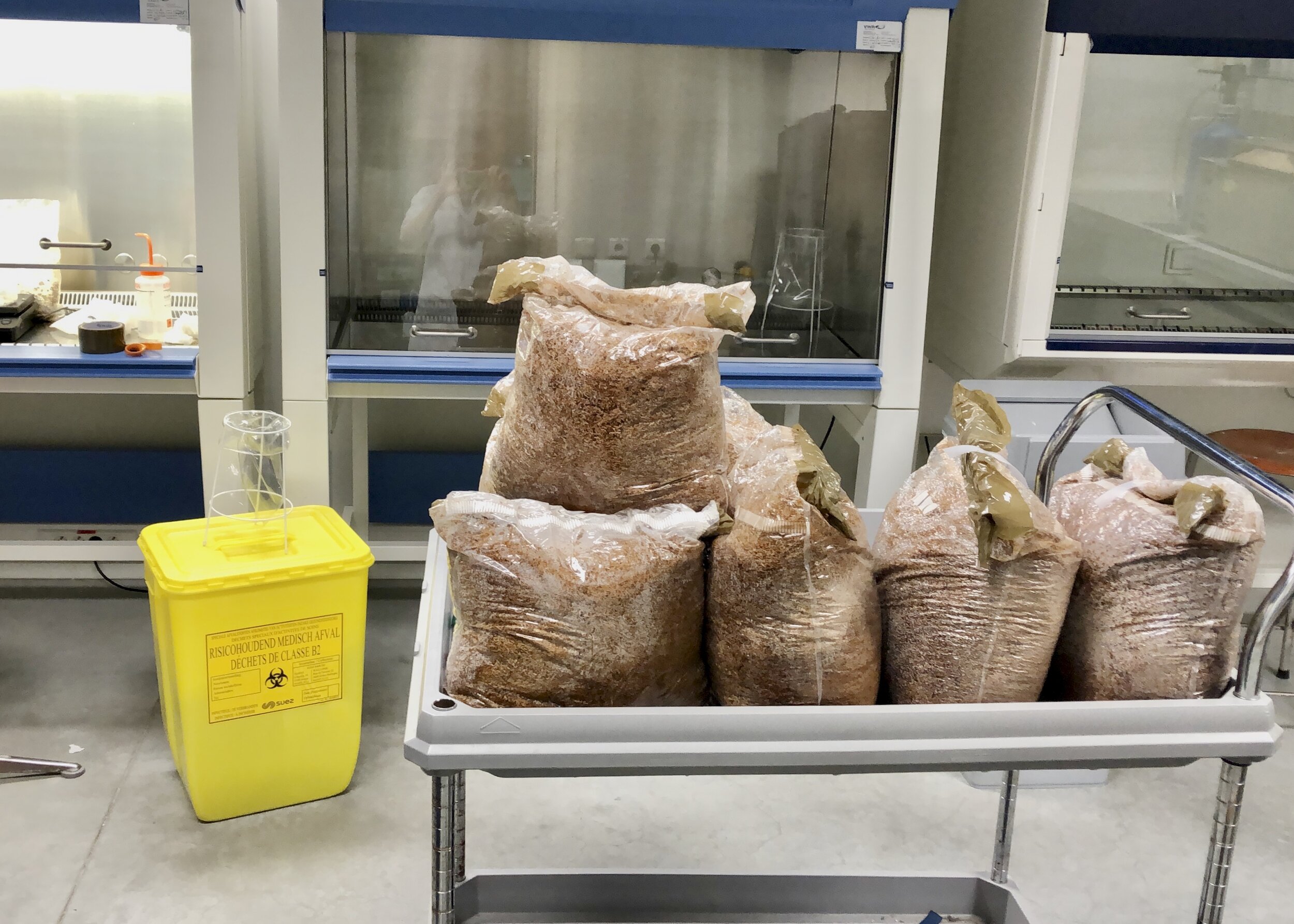
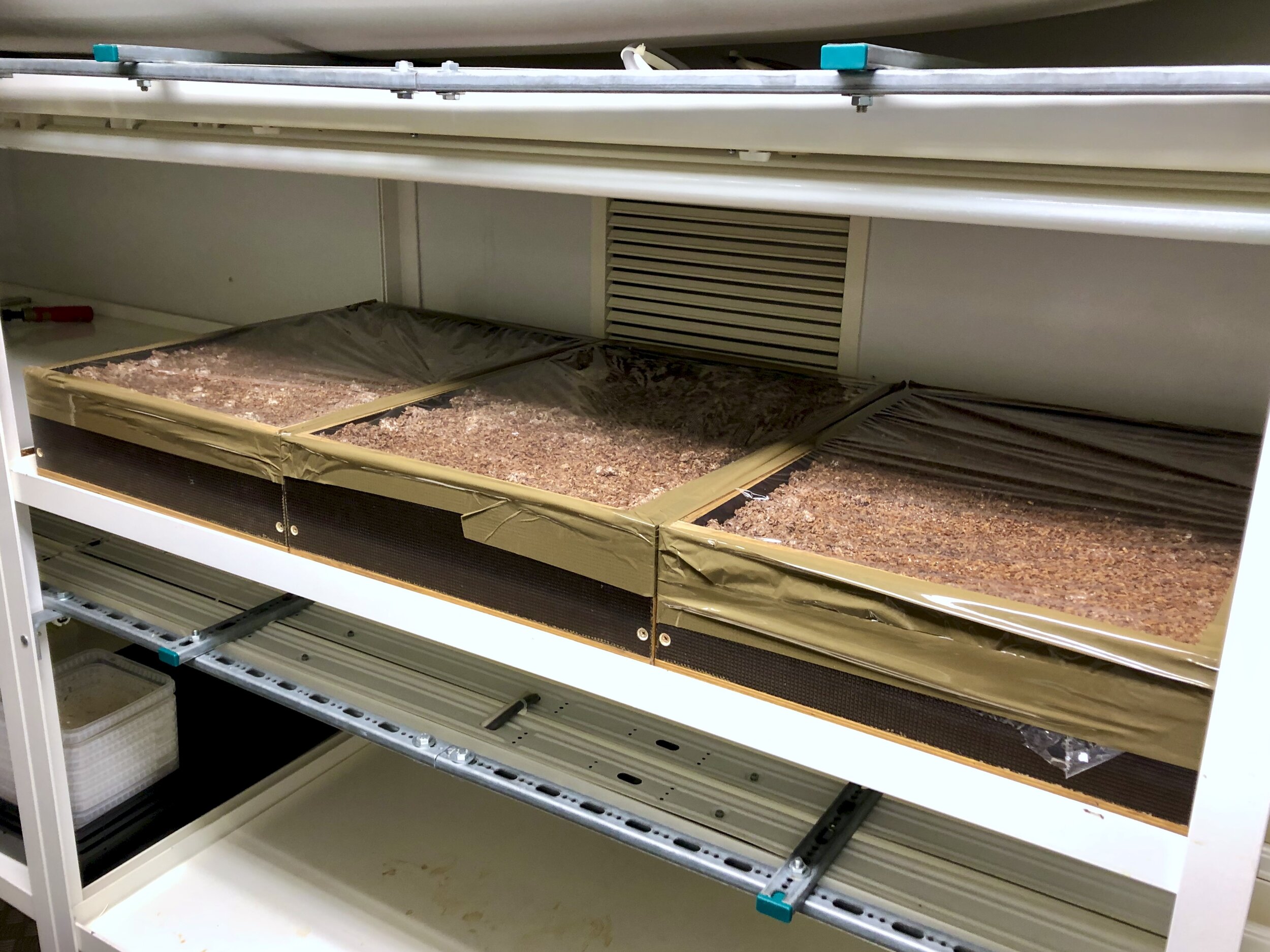
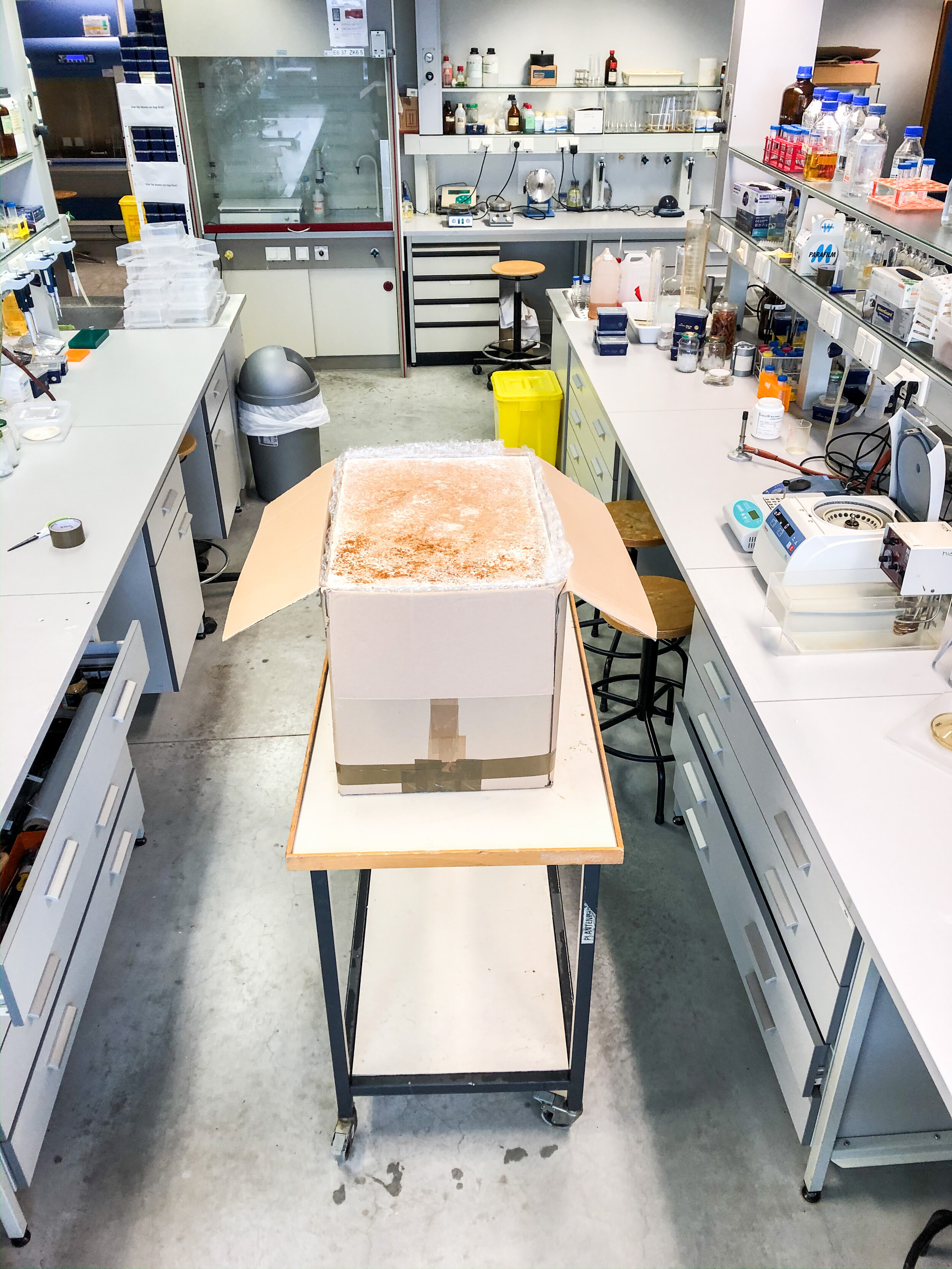
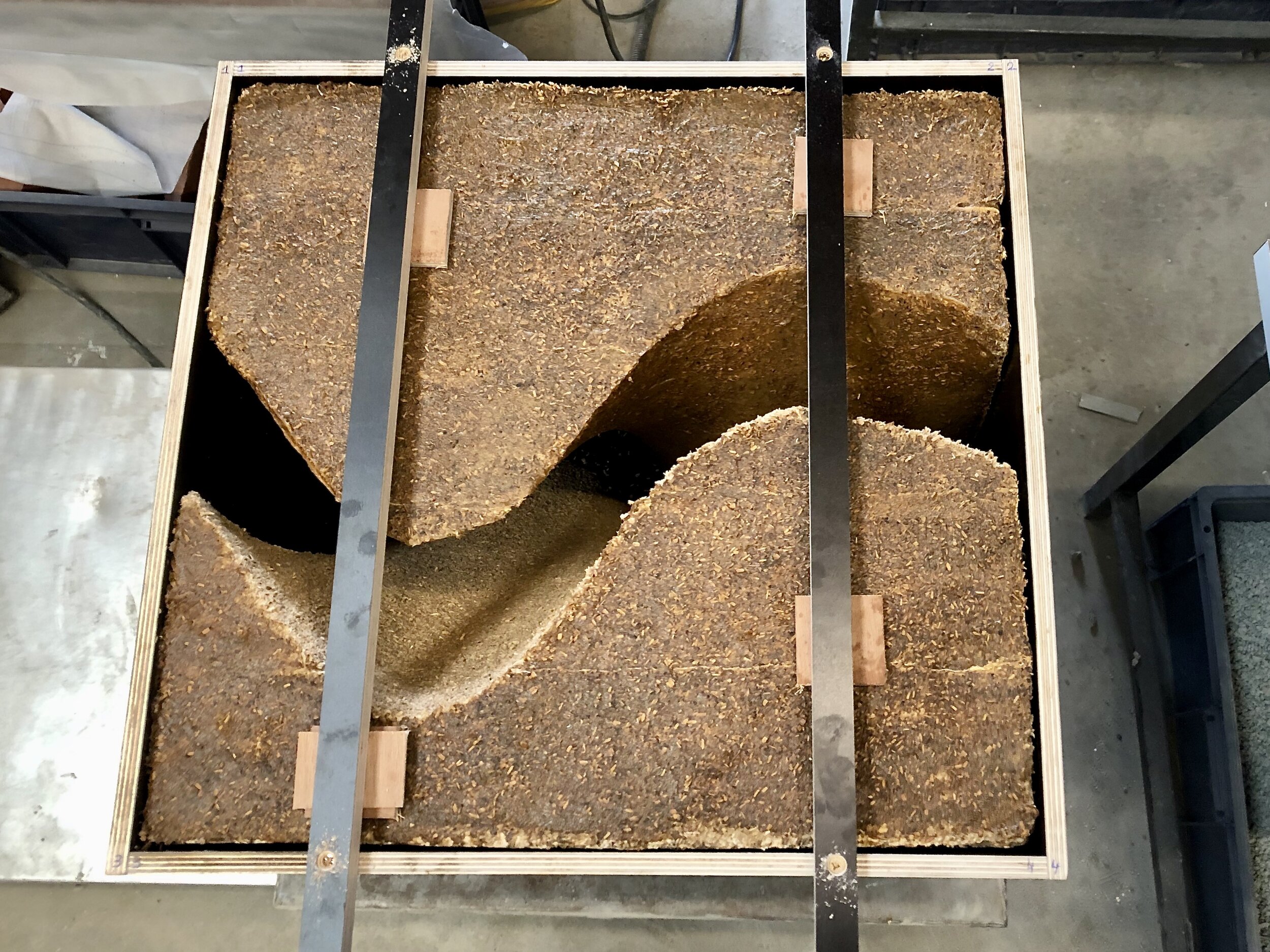
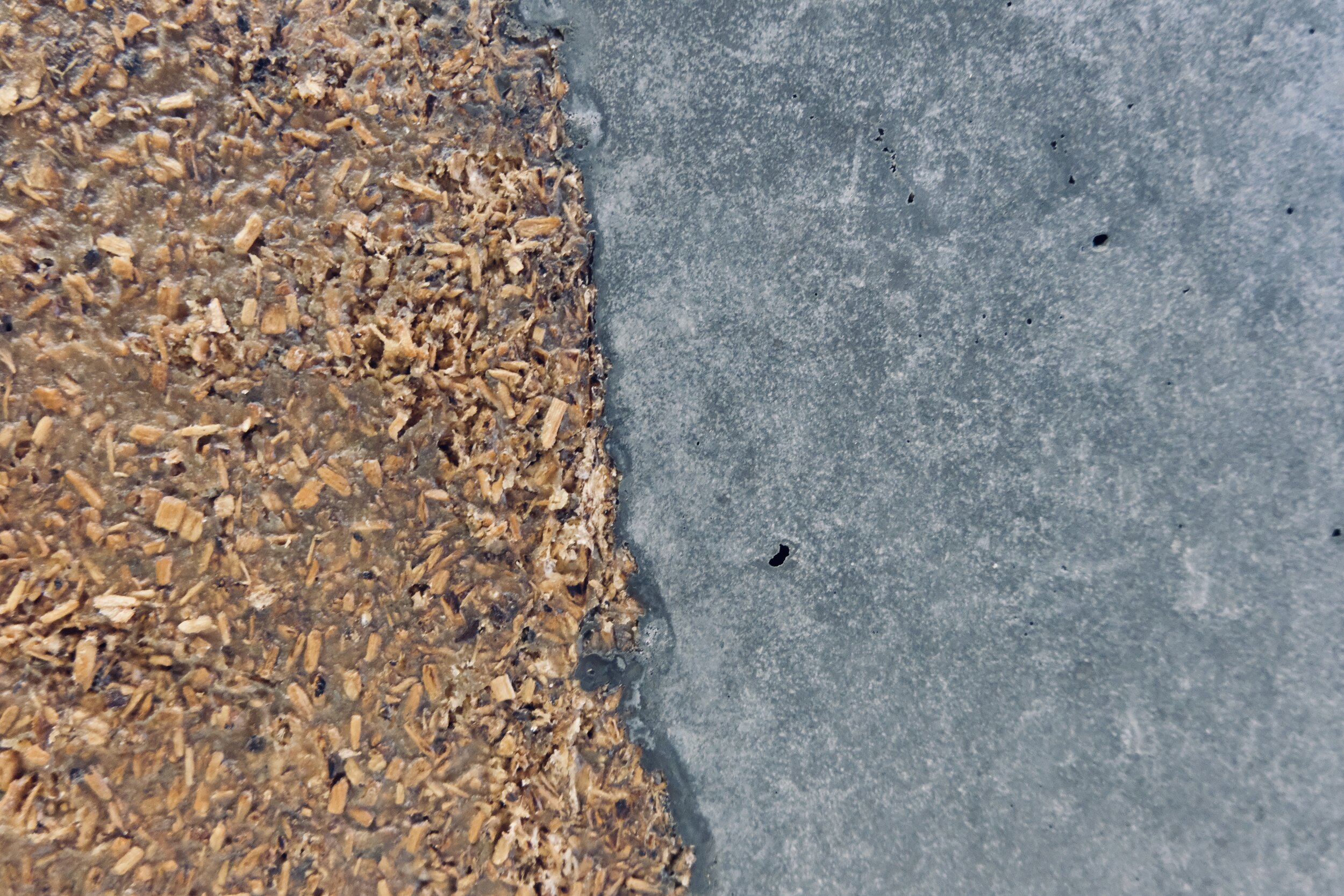
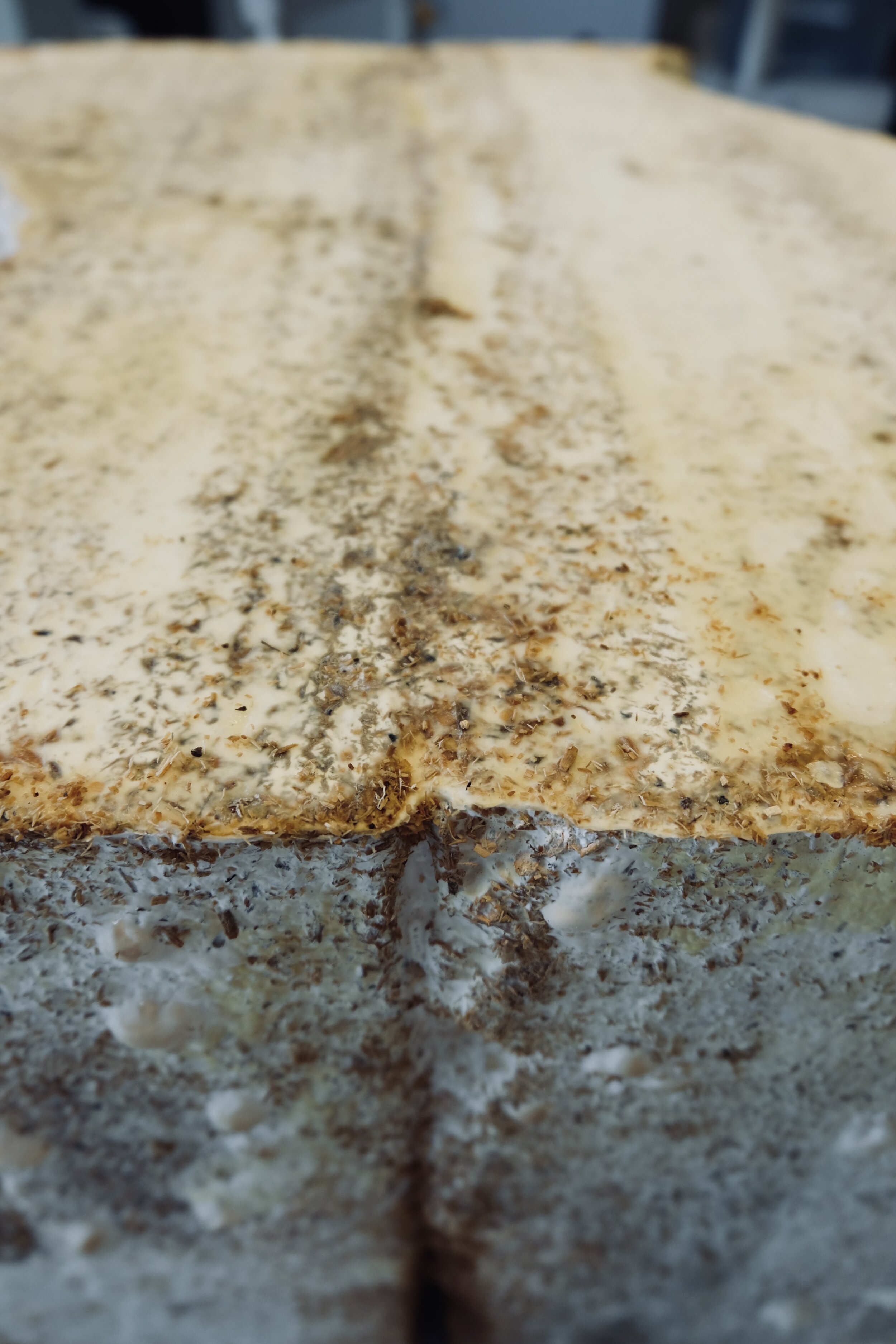
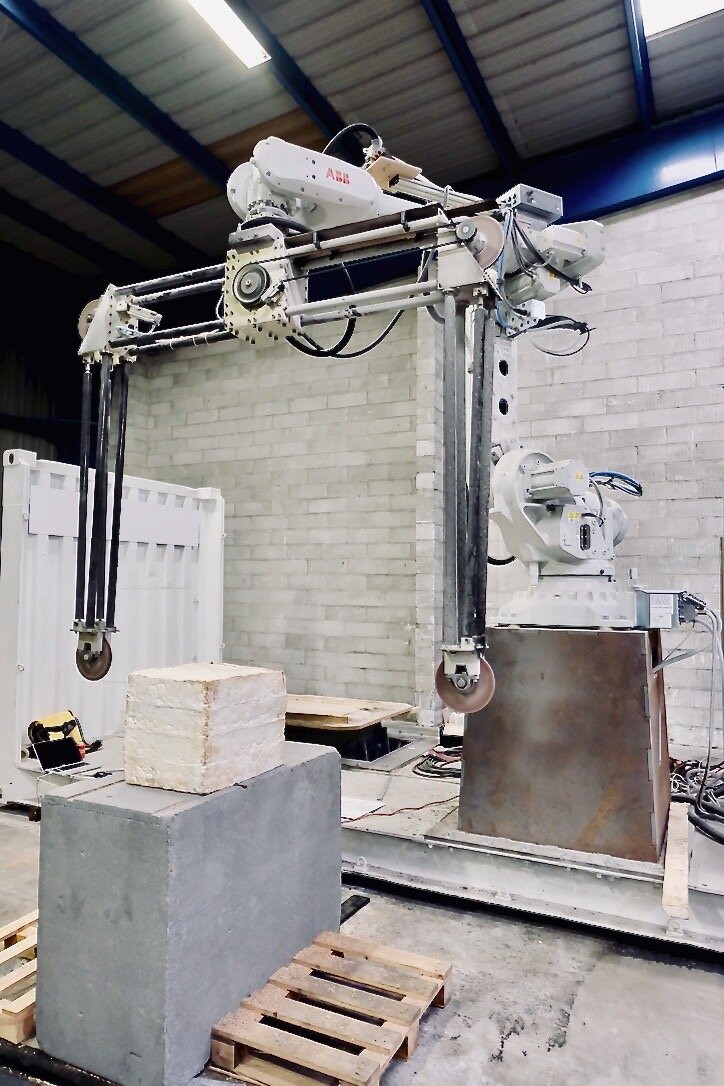
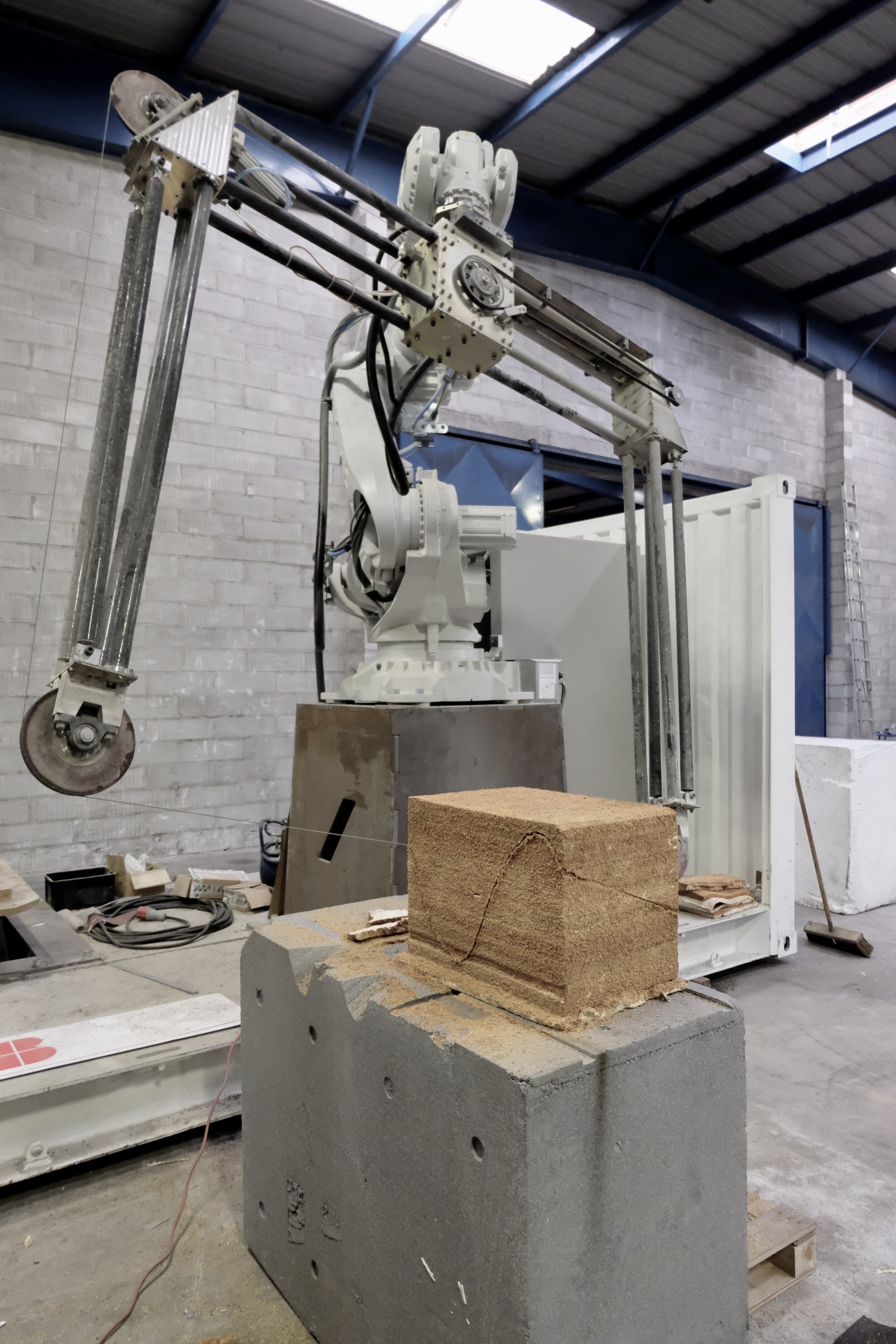
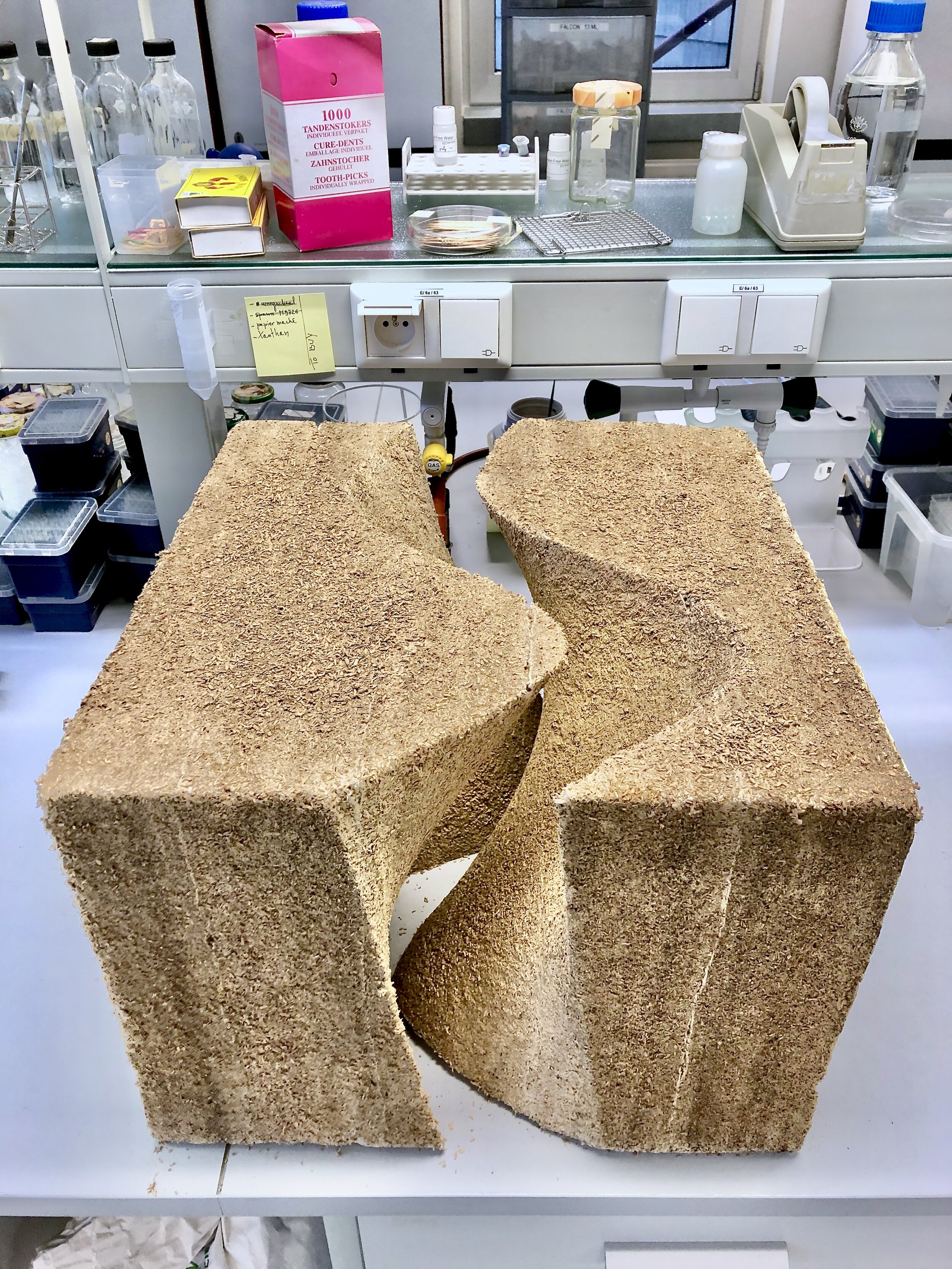